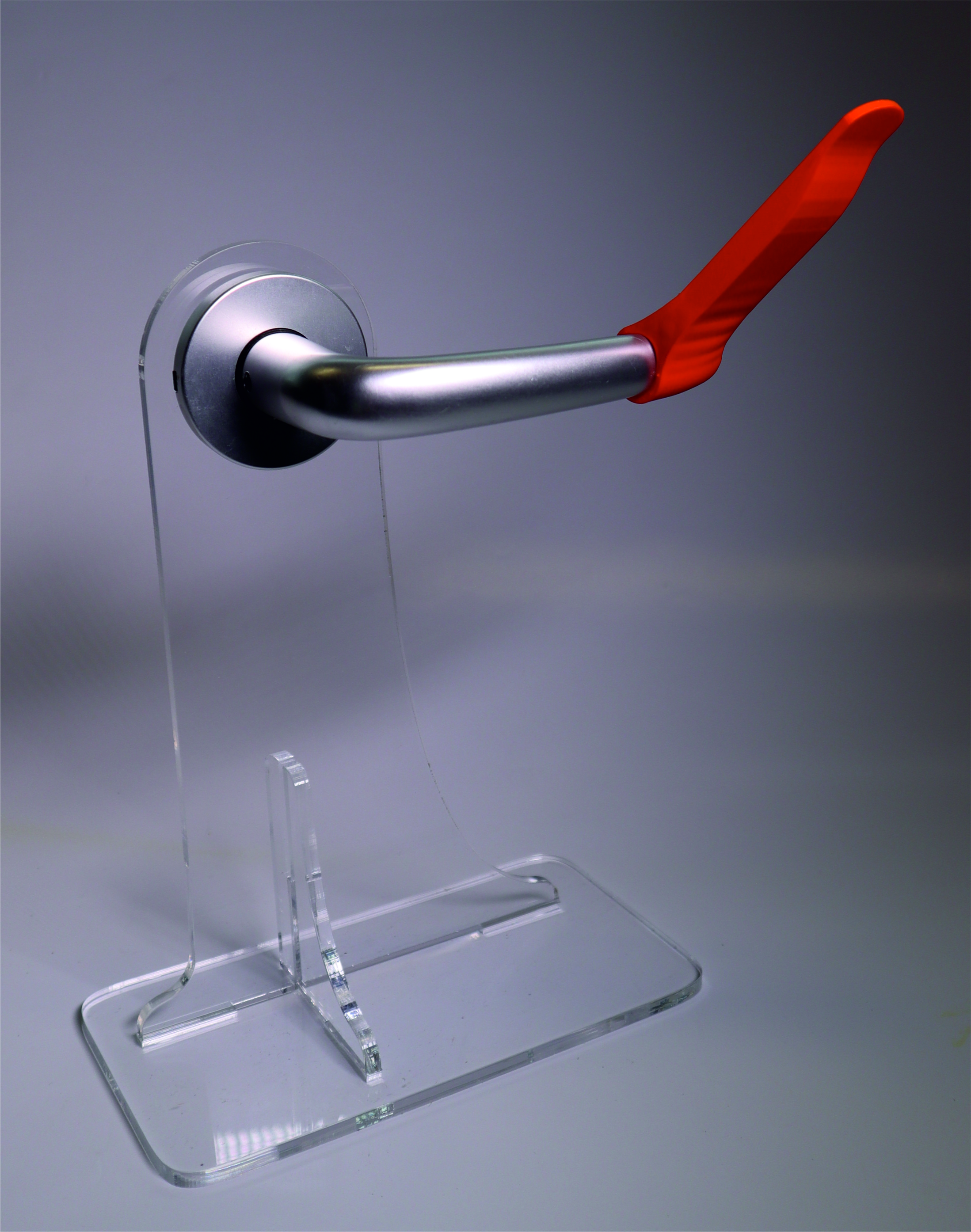
Shape memory polymers (SMPs) can assume a temporary shape after thermomechanical treatment (programming), followed by the recovery of the permanent shape upon exposure to an appropriate external stimulus. However, common thermomechanical treatment methods rely on the use of complex experimental setups for temperature conditioning and to apply forces to SMPs in a controlled manner. This contribution follows a pure material approach that takes advantage of four-dimensional (4D) printing. Fused filament fabrication is used as additive manufacturing technique to produce a thermoresponsive tool from a polyether urethane (PEU) having a glass transition temperature close to 55 °C as determined by differential scanning calorimetry (DSC). Once 4D-printed, the cylindrical shaped object was placed on a sample of laser cut shape memory polyurethane foam, whose DSC peak temperature of soft segmental melting was about 57 °C. Heating the cylinder with the foam inside of it to 75 °C and keeping that temperature constant for 15 min resulted in the compression of the foam, since the PEU released its internal stress. Upon cooling to –15 °C and thus below the peak temperature for soft segmental crystallization of 37 °C, the foam was fixed in its new shape. After 900 days of storage at temperatures close to 23 °C, the foam recovered its original shape upon reheating to 75 °C. In another experiment a 4D-printed cylinder was put into hibernation for 900 days before its thermoresponsiveness was investigated. Looking ahead, 4D-printed tools can be used not only for programming shape memory polymer foams but also for other programmable materials, thus expanding the technical application possibilities of 4D printing.
Institute:
Fraunhofer IAP
Contact:
Thorsten Pretsch, thorsten.pretsch@iap.fraunhofer.de